The Complete 3D Printer Troubleshooting Guide
- Elle
- May 30
- 5 min read
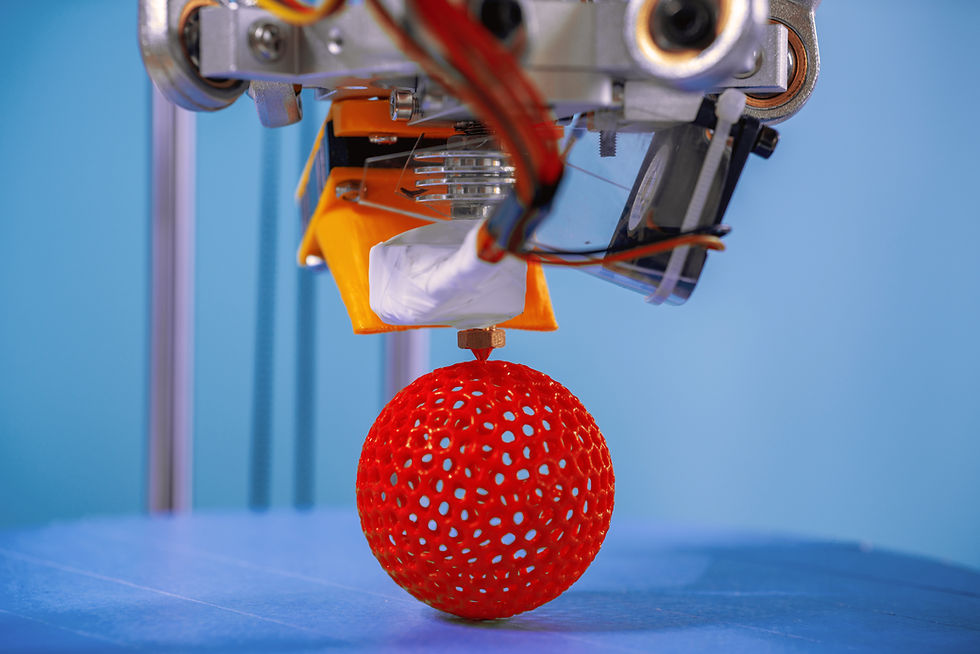
3D printing can be incredibly rewarding, but even experienced makers encounter frustrating issues. This comprehensive troubleshooting guide covers the most common problems and their solutions, organized by symptoms to help you quickly identify and fix issues.
Print Quality Issues
Poor Bed Adhesion / First Layer Problems
Symptoms: Print doesn't stick to bed, corners lift, first layer is uneven or too thin
Solutions:
Level your bed properly - Use a piece of paper to check nozzle distance at multiple points. The nozzle should barely touch the paper with slight resistance
Clean the print surface - Use isopropyl alcohol (70%+) to remove oils and residue
Adjust nozzle height - Too far = poor adhesion, too close = nozzle drags through filament
Use bed adhesion aids - Glue stick, hairspray, or blue painter's tape for difficult materials
Heat the bed - PLA: 50-60°C, ABS: 80-100°C, PETG: 70-80°C
Slow down the first layer - Reduce speed to 15-25 mm/s for better adhesion
Increase first layer extrusion - Try 105-110% extrusion multiplier for first layer only
Stringing and Oozing
Symptoms: Thin plastic strings between parts, blobs on the surface
Solutions:
Enable retraction - Set retraction distance (1-6mm for direct drive, 4-8mm for Bowden)
Increase retraction speed - Try 25-45 mm/s
Lower printing temperature - Reduce by 5-10°C increments
Increase travel speed - 120-200 mm/s for non-print moves
Enable "coasting" - Stop extruding slightly before the end of the perimeter
Tune linear advance (if available) - Helps with pressure control
Layer Shifting
Symptoms: Layers offset horizontally, creating a "staircase" effect
Solutions:
Check belt tension - Belts should be tight but not over-tensioned (guitar string tight)
Verify stepper motor connections - Ensure all connectors are secure
Reduce printing speed - High speeds can cause motors to skip steps
Check for obstructions - Ensure axes move freely without binding
Examine pulleys - Tighten grub screws on motor pulleys
Lower acceleration settings - Reduce rapid direction changes
Under-Extrusion
Symptoms: Thin walls, gaps in layers, weak prints
Solutions:
Check filament diameter - Measure with calipers and update slicer settings
Increase extrusion multiplier - Start with 105% and adjust in 2-5% increments
Clean or replace nozzle - Partial clogs reduce flow
Check extruder tension - Too loose = slipping, too tight = grinding filament
Verify temperature - Too low causes high viscosity and poor flow
Examine the Bowden tube - Replace if worn or create friction
Over-Extrusion
Symptoms: Rough surfaces, blobs, dimensions too large
Solutions:
Reduce extrusion multiplier - Try 95% and adjust downward
Lower printing temperature - Reduce by 5-10°C
Increase printing speed - Gives less time for over-extrusion
Check filament diameter - Thicker filament causes over-extrusion
Calibrate E-steps - Ensure the extruder pushes the correct amount of filament
Mechanical Issues
Clogged Nozzle
Symptoms: No extrusion, inconsistent flow, grinding sounds from the extruder
Solutions:
Cold pull method - Heat to printing temp, insert filament, cool to 90°C, pull firmly
Needle/wire cleaning - Use 0.4mm wire or acupuncture needle (nozzle off and cool)
Acetone soak - For ABS/HIPS clogs (remove nozzle first)
Heat up and push - Manually push filament through at printing temperature
Replace nozzle - Sometimes easier than cleaning severely clogged nozzles
Extruder Problems
Symptoms: Clicking/grinding sounds, filament not feeding, inconsistent extrusion
Solutions:
Adjust extruder tension - Should grab filament firmly without crushing
Clean extruder gear - Remove filament debris from drive gear teeth
Check filament path - Ensure smooth path from spool to hotend
Replace worn components - Drive gears and tensioners wear out over time
Verify motor function - Test the extruder motor independently
Heating Issues
Symptoms: Temperature fluctuations, heating failures, thermal runaway errors
Solutions:
Check thermistor connections - Loose connections cause temperature readings issues
Verify heater cartridge - Test resistance and connections
PID tuning - Calibrate temperature control for stable heating
Insulate the hotend - Silicone socks help maintain a consistent temperature
Replace failing components - Thermistors and heater cartridges eventually fail
Print Defects
Warping
Symptoms: Corners or edges curl upward, especially on large prints
Solutions:
Use heated bed - Essential for ABS, helpful for other materials
Add enclosure - Maintains ambient temperature around the print
Use brim or raft - Increases surface area for bed adhesion
Reduce bed temperature gradually - Let prints cool slowly
Design considerations - Avoid large flat surfaces, add mouse ears to corners
Z-Banding
Symptoms: Horizontal lines or ridges at regular intervals
Solutions:
Check Z-axis components - Tighten loose couplers, replace bent lead screws
Lubricate Z-axis - Use appropriate lubricant for smooth operation
Verify layer height - Should be a multiple of Z-axis step resolution
Check bed tramming - Uneven bed can cause banding patterns
Examine motor mounts - Loose motors cause inconsistent movement
Elephant's Foot
Symptoms: The first layer is wider than the subsequent layers
Solutions:
Reduce bed temperature - Lower by 5-10°C after the first few layers
Adjust first layer height - Slightly increase nozzle distance
Add a chamfer in the design - 45° angle on the bottom edges
Enable "elephant's foot compensation" - Available in some slicers
Reduce first layer extrusion - Try 95% for the first layer only
Software and Settings
Slicer Settings Optimization
Common setting ranges:
Layer height: 0.1-0.3mm (0.2mm standard)
Print speed: 40-80 mm/s (slower for details)
Infill: 10-20% for most prints
Wall thickness: 2-4 perimeters (0.8-1.6mm total)
Temperature guidelines:
PLA: 190-220°C hotend, 50-60°C bed
ABS: 220-250°C hotend, 80-100°C bed
PETG: 220-250°C hotend, 70-80°C bed
TPU: 210-230°C hotend, 20-60°C bed
Calibration Procedures
Essential calibrations:
Bed leveling - Critical for first layer success
E-steps calibration - Ensures accurate extrusion amounts
Flow rate tuning - Fine-tunes extrusion for material/nozzle combination
Temperature towers - Find optimal temperature for each filament
Retraction tuning - Eliminates stringing without under-extrusion
Maintenance Tips
Regular Maintenance Schedule
Weekly:
Clean the print bed surface
Check belt tension
Clear any debris from the fans
Monthly:
Lubricate moving parts
Check all connections
Clean the extruder drive gear
Verify bed level
As needed:
Replace worn nozzles
Update firmware
Calibrate after hardware changes
Replace PTFE tubing (Bowden setups)
Preventive Measures
Store filament properly - Sealed containers with desiccant
Keep the printer clean - Dust affects print quality and component life
Use quality filament - Poor filament causes most printing problems
Monitor first layers - Catch problems early
Keep spare parts - Nozzles, belts, and thermistors commonly fail
Quick Diagnostic Flowchart
Print won't start? → Check bed level → Verify temperatures → Test extrusion manually
Poor surface quality? → Check layer height → Verify speeds → Examine temperatures
Print fails mid-way? → Check filament supply → Verify bed adhesion → Examine for clogs
Dimensional inaccuracy? → Calibrate E-steps → Check belt tension → Verify slicer settings
Remember: 3D printing requires patience and systematic troubleshooting. Change one variable at a time, document what works, and don't be afraid to start with basic calibrations when problems arise. Once properly diagnosed, most issues have straightforward solutions.
Comments